Aluminium welding revolutionises prototype building in the area of electric mobility
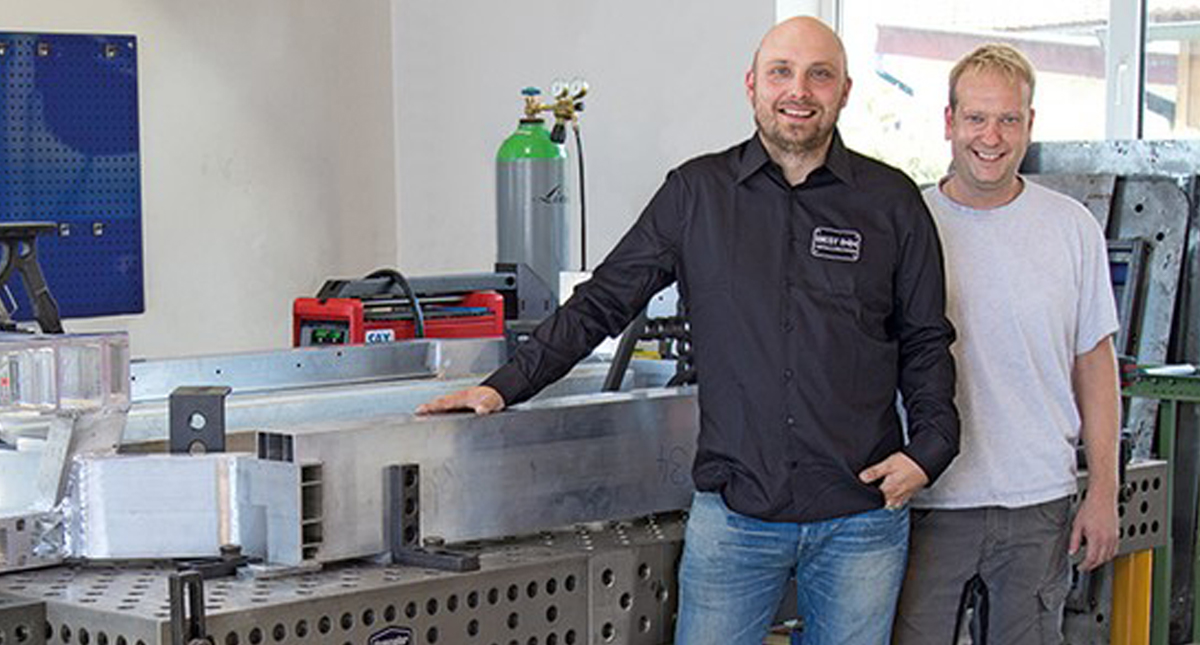
If you always thought that start-ups were only involved in software and the internet, etc., you need to read this article! On a hot summers day, we paid a visit to the company BEST Inn in Roding, Germany. As we arrived at the modern company premises and production building in temperatures of 35 degrees, we were greeted by two cheerful young men, Stefan Breu and Thomas Eckl, the founders and managing directors of BEST Inn.
Mr Eckl / Mr Breu: We are delighted that you have made it to our company.
DEMMELER: The pleasure is all ours. Thank you for the invitation. How is it that in such a short space of time – after all, BEST Inn has been in existence for barely three years – you are approached by leading car manufacturers for building electric vehicle prototypes?
Mr. Eckl / Mr. Breu: With a smile on his lips, Thomas Eckl recounts: Thank to our expertise in the area of aluminium welding, we have been able to revolutionise prototype building of structures for electric vehicles. Where previously expensive thermoforming was required to produce individual parts, we have been able to create a steel construction with the same tolerances and the same levels of precision.
DEMMELER: What does that mean for car manufacturers?
Mr. Eckl / Mr. Breu: Where previously it cost approx. 120,000 EUR to produce one car chassis, we can now do it for about a quarter of the price. And where precision is continued, we are continuously making progress. We use various methods to compensate for welding distortion. These methods range from using the right device, to keeping the temperature of the device and components stable during the machining process. DEMMELER’s advice and products have been an enormous help in the process.
DEMMELER: We’re delighted to hear it.
Mr. Eckl / Mr. Breu: To be even more precise, about two years ago we purchased a welding table. We were already well-impressed with the system. But after a visit by one of your sales reps, who gave us advice, we understood how to use your products correctly, and together with our expertise, this helped us to make a quantum leap. We have only been using DEMMELER clamping systems ever since. We no longer use our first welding table (editor’s comment: made by another manufacturer).
DEMMELER: How do you explain your leading technical edge?
Mr Eckl: When it comes to aluminium welding, there’s no one like us. Thanks to DEMMELER’s 3D system and excellent advice, we can achieve a level of precision that is unrivalled by anyone else. For example, we reduce welding distortion by heating the device and the work piece to a minimum. The optimum material qualities of DEMMELER’s welding table are an enormous help in the process. It’s a well-known fact that DEMMELER offers the best tools and accessories – and we’re not just talking about the polygon bolt.
DEMMELER: However, your customers don’t just come from the car manufacturing industry do they?
Mr Breu: That’s right. Our customers come from a whole range of other fields. One of the things they appreciate about us the most is the fact that we are extremely fast. And we don’t just deal with order production. We also provide support through constructive solutions. We create drawings and constructions in extremely short time scales and offer the most cost-effective solutions.
Mr Eckl: All the same, it’s definitely something special when we’re visited by leading sports car manufacturers. We receive visits from all kinds of masterminds, from developers to the board members of leading vehicle manufacturers. It can be very impressive when 10 or 15 top vehicles are parked in our yard at once – usually you only ever get to see one or two cars of this type on the motorway every now and then.
DEMMELER: And what are your plans for the future?
Mr Eckl / Mr Breu: We can’t complain. We’ve just received a new order from an Italian sports car manufacturer. We plan to start working on the prototype construction for this at the end of 2016/start of 2017. Of course, we’ll again be relying on our partnership with DEMMELER. We intend to use your PP28 system for this.